February, 2025
now browsing by month
The Impact of Curing Temperature on the Performance of Powder Coatings
In the world of powder coatings, achieving the perfect finish is a delicate balance of various factors, with curing temperature playing a pivotal role. While many articles discuss the general applications and benefits of powder coatings, this piece delves into the specific influence of curing temperature on the performance and durability of powder-coated surfaces. Understanding this relationship is crucial for industries seeking to optimize their coating processes for both quality and efficiency. The Basics of Powder Coating Curing Powder coating is a dry finishing process that uses finely ground particles of pigment and resin, which are electrostatically charged and sprayed onto a surface. The coated item is then heated, causing the powder to melt, flow, and form a durable finish. The curing process is where the magic happens, transforming the powder into a solid, protective layer. Curing temperature is one of the most critical parameters in this process. It determines not only the time required for curing but also the final properties of the coating, including its hardness, adhesion, and resistance to environmental factors. Optimal Curing Temperature: A Delicate Balance The optimal curing temperature for powder coatings typically ranges between 160°C to 200°C (320°F to 392°F), depending on the specific formulation of the powder. However, achieving the right temperature is a balancing act. Too low a temperature can result in under-cured coatings, which may exhibit poor adhesion, reduced hardness, and diminished chemical resistance. On the other hand, excessively high temperatures can lead to over-curing, causing the coating to become brittle, discolored, or even degrade over time. Effects of Curing Temperature on Coating Properties 1.Adhesion: The curing temperature directly affects the adhesion of the coating to the substrate. Proper adhesion is crucial for the longevity of the coating. If the temperature is too low, the powder may not fully melt and bond with the surface, leading to poor adhesion. Conversely, too high a temperature can cause the coating to cure too quickly, preventing adequate adhesion. 2.Hardness and Durability: Higher curing temperatures generally result in harder coatings, which are more resistant to scratches and wear. However, if the temperature is too high, the coating may become overly brittle, making it susceptible to cracking under stress. 3.Chemical Resistance: The curing temperature also influences the chemical resistance of the coating. Under-cured coatings may not withstand exposure to chemicals as well as those that are properly cured. Achieving the right temperature ensures that the coating forms a robust, impervious layer that can resist chemical attack. 4.Color and Gloss: Temperature fluctuations can affect the color and gloss of the final finish. Over-curing can lead to discoloration or a loss of gloss, while under-curing may result in a finish that appears uneven or lacks the desired sheen. Optimizing the Curing Process To optimize the curing process, manufacturers must carefully control the temperature and duration of the curing cycle. This can be achieved through the use of advanced curing ovens equipped with precise temperature control systems. Additionally, regular monitoring and calibration of equipment are essential to ensure consistent results. Conclusion The curing temperature is a critical factor in determining the performance and durability of powder coatings. By understanding and controlling this variable, manufacturers can achieve high-quality finishes that meet the stringent demands of various industries. Whether it’s for automotive parts, household appliances, or industrial machinery, getting the curing temperature right is key to ensuring the longevity and aesthetic appeal of powder-coated surfaces. In summary, while powder coatings offer numerous benefits, the curing temperature is the linchpin that determines their ultimate success. By mastering this aspect of the process, companies can enhance the quality and reliability of their coated products, ultimately leading to greater customer satisfaction and improved market competitiveness.
The Impact of Particle Size Distribution on the Performance of Powder Coatings
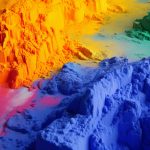
In the world of powder coatings, achieving the perfect finish is a blend of art and science. While the aesthetic and protective qualities of powder coatings are well-documented, one critical factor that significantly influences their performance is often overlooked: particle size distribution. This article delves into how the particle size distribution of powder coatings affects their application, finish quality, and overall performance, providing insights that can help professionals optimize their coating processes. Understanding Particle Size Distribution Particle size distribution (PSD) refers to the range and frequency of different particle sizes in a powder coating. It is typically measured in microns and can vary significantly depending on the manufacturing process and the intended application of the coating. A typical powder coating might have a PSD ranging from 1 to 100 microns, but the majority of particles usually fall within a narrower range. The PSD is crucial because it directly impacts how the powder flows, charges, and adheres during the application process. It also influences the final appearance and durability of the coating. Application Efficiency One of the most immediate effects of PSD is on the application efficiency. Finer particles (typically below 10 microns) are more likely to be overcharged and can lead to issues like “back ionization,” where the powder layer repels incoming particles, resulting in an uneven coating. On the other hand, larger particles (above 70 microns) may not charge efficiently and can lead to poor transfer efficiency, meaning more powder is wasted during application. Optimizing the PSD can significantly enhance transfer efficiency, ensuring that more powder adheres to the substrate and less is lost as overspray. This not only improves the cost-effectiveness of the process but also reduces environmental impact by minimizing waste. Finish Quality The PSD also plays a critical role in determining the finish quality of the coating. A narrow PSD, where most particles are of a similar size, generally results in a smoother, more uniform finish. This is because particles of similar size tend to melt and flow evenly during the curing process, creating a consistent surface. Conversely, a broad PSD with a wide range of particle sizes can lead to a textured finish. While this can be desirable for certain applications, such as those requiring a matte or textured appearance, it can be detrimental for applications requiring a high-gloss, smooth finish. Durability and Performance The durability of a powder coating is influenced by its ability to form a continuous, defect-free film. A well-distributed PSD helps in achieving this by ensuring that particles melt and flow together seamlessly. Finer particles can fill in the gaps between larger particles, resulting in a more cohesive film. Moreover, a balanced PSD can enhance the coating’s resistance to environmental factors such as UV radiation, moisture, and chemicals. This is particularly important for outdoor applications where the coating is exposed to harsh conditions. Optimizing Particle Size Distribution To optimize the PSD for a specific application, manufacturers can employ various techniques, including: 1.Air Classification: This method separates particles based on their size and density, allowing for the production of powders with a more uniform PSD. 2.Milling and Grinding: These processes can be used to reduce the size of larger particles, thereby narrowing the PSD. 3.Blending: Mixing powders with different PSDs can help achieve a desired distribution for specific applications. In conclusion, the particle size distribution of powder coatings is a critical factor that impacts their application, finish quality, and overall performance. By understanding and optimizing the PSD, manufacturers and applicators can achieve superior coating results, enhancing both the aesthetic and protective qualities of the finish. As the demand for high-performance coatings continues to grow, paying attention to PSD will be more important than ever in meeting the needs of diverse applications. By focusing on the nuances of particle size distribution, professionals can unlock the full potential of powder coatings, ensuring that they not only meet but exceed the expectations of their clients.
Emerging Technologies Shaping the Future of Powder Coatings
The powder coatings industry is undergoing a transformative phase, driven by technological advancements and the global push toward sustainability. While traditional applications of powder coatings in automotive, construction, and appliance industries are well-documented, the next frontier lies in cutting-edge innovations that redefine performance, efficiency, and environmental impact. This article explores the latest technological breakthroughs and their implications for the future of powder coatings. 1. UV and IR Curing: Revolutionizing Efficiency UV (ultraviolet) and IR (infrared) curing technologies are emerging as game-changersRead More …
The Future of Powder Coatings: Smart and Functional Coatings
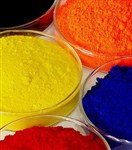
The powder coating industry is undergoing a quiet revolution. While traditional powder coatings have long been valued for their durability, eco-friendliness, and cost-effectiveness, a new generation of smart and functional coatings is pushing the boundaries of what’s possible. These advanced coatings are not just protective layers; they’re transforming surfaces into interactive, intelligent, and multifunctional interfaces. 1. Self-Healing Coatings: The Next Frontier Imagine a world where scratches on your car or appliances disappear on their own. Self-healing powder coatings are makingRead More …