Archives
now browsing by author
How Low-Cure Powder Coatings Are Revolutionizing Temperature-Sensitive Substrates
The coatings industry is witnessing a quiet revolution as low-cure powder coatings redefine what’s possible with heat-sensitive materials. Unlike traditional powder coatings requiring 180-200°C cure temperatures, these advanced formulations achieve full crosslinking at 120-140°C – a breakthrough enabling metal decorators, wood manufacturers, and automotive suppliers to expand into new markets. The Physics Behind the Innovation Low-cure formulations rely on catalytic hybrid systems combining epoxy-carboxy reactions with specialized accelerators. The real game-changer lies in the use of β-hydroxyalkylamide (HAA) curing agentsRead More …
Solving the 5 Most Frustrating Powder Coating Defects (And How to Prevent Them for Good)
Every powder coating professional knows that sinking feeling when a flawless finish seems impossible. Despite 78% of industrial manufacturers now using thermosetting powders (Grand View Research, 2023), recurring defects still cost the industry over $420 million annually in rework. After troubleshooting coating issues in over 200 facilities, I’ve identified patterns behind five persistent problems – and more importantly, their science-backed solutions. 1. The Orange Peel Paradox: When Smooth Goes WrongThat textured surface resembling citrus skin often stems from conflicting factors.Read More …
Bio-Based Powder Coatings: Bridging Sustainability and High Performance
As industries scramble to meet net-zero targets, a quiet revolution is unfolding in the powder coating sector: plant-derived resins are replacing petroleum-based chemistries without compromising performance. Unlike generic “eco-friendly” claims, bio-based powder coatings offer measurable advantages that resonate with both manufacturers and ESG auditors. The Science Behind Bio-Based Formulations Bio-based powders utilize renewable resources like: Soybean oil esters for flexible film formation Lignin from wood pulp as a crosslinking agent Terpene resins (from citrus waste) enhancing UV resistance A 2023 study in Coatings Technology Journal revealed thatRead More …
Why Powder-Coated Aluminum is Revolutionizing Sustainable Architectural Design
In the quest for durable, eco-friendly, and visually striking building materials, architects and developers are increasingly turning to powder-coated aluminum. This specialized finishing method isn’t just a buzzword—it’s reshaping modern construction by solving critical challenges like corrosion resistance, color retention, and environmental compliance. Let’s explore why this combination is becoming the gold standard for high-performance architectural projects. 1. The Science Behind Corrosion Resistance Aluminum’s natural oxide layer already offers decent protection, but powder coating takes it to the next level. UnlikeRead More …
Why Surface Pretreatment is the Make-or-Break Stage in Powder Coating
While most discussions about powder coating focus on application techniques or environmental benefits, professionals know that 90% of coating failures stem from what happens before the powder even leaves the gun. Surface pretreatment remains the most underestimated yet critical phase in achieving durable, high-quality finishes. The Science Behind the SurfaceMetal surfaces naturally develop oxides, oils, and microscopic imperfections that no powder coating can properly adhere to. A 2022 study by the Powder Coating Institute revealed that proper pretreatment improves coating adhesion byRead More …
Optimizing Powder Coating Curing Processes for Enhanced Efficiency and Sustainability
In the evolving landscape of surface finishing, powder coatings have cemented their reputation as a durable, cost-effective, and eco-friendly solution. While much has been written about their benefits and general applications, one often overlooked yet critical aspect lies in the curing process—the stage where applied powder transforms into a resilient finish. For manufacturers and applicators, refining curing techniques can unlock significant improvements in energy efficiency, production speed, and environmental impact. Let’s dive into advanced strategies for optimizing powder coating curing toRead More …
Optimizing Curing Processes for Durable Powder Coating Finishes
While powder coatings are celebrated for their durability and eco-friendly properties, achieving consistent, high-quality finishes hinges on one critical yet often overlooked step: the curing process. For manufacturers and applicators, refining curing parameters isn’t just about adhering to specifications—it’s a science that balances energy efficiency, film integrity, and long-term performance. Why Curing Matters More Than You Think Curing transforms powder from a loosely adhered layer into a continuous, cross-linked film. However, variations in substrate materials, oven designs, and powder chemistriesRead More …
Understanding the Role of Curing Mechanisms in Powder Coating Performance
In the world of industrial finishing, powder coating has emerged as a popular choice due to its durability, efficiency, and environmental benefits. While many articles discuss the general aspects of powder coating, such as its applications and benefits, this piece delves into a more specific and critical aspect: the curing mechanisms and their impact on the overall performance of powder coatings. The Basics of Powder Coating Curing Powder coating is a dry finishing process where finely ground particles of pigment and resin are electrostatically charged and sprayed onto a substrate. The coated part is then heated, causing the powder to melt, flow, and form a continuous film. The curing process is where the magic happens, transforming the powder into a durable coating through chemical reactions. There are primarily two types of curing mechanisms in powder coatings: thermal curing and UV curing. Each has its unique characteristics and advantages, influencing the coating’s final properties. 1. Thermal Curing: The Traditional Approach Thermal curing, also known as thermosetting, is the most common method used in powder coating. This process involves exposing the coated part to elevated temperatures, typically between 150°C to 200°C (302°F to 392°F), for a specific period. The heat initiates a cross-linking reaction between the resin and the curing agent, resulting in a hard, durable finish. Key Factors in Thermal Curing: Temperature and Time: The curing temperature and dwell time are crucial. Insufficient temperature or time can lead to under-cured coatings, which may exhibit poor adhesion, low hardness, and reduced chemical resistance. Conversely, over-curing can cause discoloration, brittleness, and degradation of the coating. Oven Design: The design of the curing oven plays a significant role in achieving uniform curing. Proper air circulation and temperature control are essential to ensure consistent coating quality. Material Compatibility: Not all materials can withstand the high temperatures required for thermal curing. Substrates like certain plastics and wood may warp or degrade, limiting the application of thermosetting powder coatings. 2. UV Curing: The Innovative Alternative UV curing is a relatively newer technology in the powder coating industry. It involves using ultraviolet light to initiate a photochemical reaction that cures the coating almost instantly. This method offers several advantages over traditional thermal curing. Advantages of UV Curing: Speed: UV curing is significantly faster than thermal curing, with curing times measured in seconds rather than minutes. This increases production efficiency and reduces energy consumption. Energy Efficiency: UV curing requires less energy, as it eliminates the need for high-temperature ovens. This makes it a more environmentally friendly option. Temperature Sensitivity: UV curing is ideal for heat-sensitive materials, such as certain plastics and wood, as it does not rely on heat to cure the coating. Challenges of UV Curing: Initial Cost: The equipment required for UV curing, such as UV lamps and specialized ovens, can be more expensive than traditional thermal curing equipment. Material Limitations: Not all powder coating formulations are compatible with UV curing. The selection of suitable materials is crucial for successful UV curing. Impact on Coating Performance The choice of curing mechanism has a profound impact on the performance of the powder coating. Thermal curing generally results in coatings with excellent chemical resistance, durability, and mechanical properties. However, it can be limiting for certain applications due to the high temperatures involved. On the other hand, UV curing offers faster processing times and is more suitable for heat-sensitive substrates. The coatings produced are typically highly resistant to scratches and have a smooth, glossy finish. However, they may not match the chemical resistance of thermally cured coatings. Conclusion Understanding the curing mechanisms in powder coating is essential for selecting the right process for your specific application. Whether you opt for the traditional thermal curing or the innovative UV curing, each method has its own set of advantages and challenges. By considering factors such as material compatibility, production speed, and energy efficiency, you can make an informed decision that enhances the performance and longevity of your powder-coated products. In the ever-evolving landscape of industrial finishing, staying informed about advancements in curing technologies can give you a competitive edge. As the demand for high-quality, durable, and environmentally friendly coatings continues to grow, the role of curing mechanisms in powder coating will only become more significant.
The Impact of Curing Temperature on the Performance of Powder Coatings
In the world of powder coatings, achieving the perfect finish is a delicate balance of various factors, with curing temperature playing a pivotal role. While many articles discuss the general applications and benefits of powder coatings, this piece delves into the specific influence of curing temperature on the performance and durability of powder-coated surfaces. Understanding this relationship is crucial for industries seeking to optimize their coating processes for both quality and efficiency. The Basics of Powder Coating Curing Powder coating is a dry finishing process that uses finely ground particles of pigment and resin, which are electrostatically charged and sprayed onto a surface. The coated item is then heated, causing the powder to melt, flow, and form a durable finish. The curing process is where the magic happens, transforming the powder into a solid, protective layer. Curing temperature is one of the most critical parameters in this process. It determines not only the time required for curing but also the final properties of the coating, including its hardness, adhesion, and resistance to environmental factors. Optimal Curing Temperature: A Delicate Balance The optimal curing temperature for powder coatings typically ranges between 160°C to 200°C (320°F to 392°F), depending on the specific formulation of the powder. However, achieving the right temperature is a balancing act. Too low a temperature can result in under-cured coatings, which may exhibit poor adhesion, reduced hardness, and diminished chemical resistance. On the other hand, excessively high temperatures can lead to over-curing, causing the coating to become brittle, discolored, or even degrade over time. Effects of Curing Temperature on Coating Properties 1.Adhesion: The curing temperature directly affects the adhesion of the coating to the substrate. Proper adhesion is crucial for the longevity of the coating. If the temperature is too low, the powder may not fully melt and bond with the surface, leading to poor adhesion. Conversely, too high a temperature can cause the coating to cure too quickly, preventing adequate adhesion. 2.Hardness and Durability: Higher curing temperatures generally result in harder coatings, which are more resistant to scratches and wear. However, if the temperature is too high, the coating may become overly brittle, making it susceptible to cracking under stress. 3.Chemical Resistance: The curing temperature also influences the chemical resistance of the coating. Under-cured coatings may not withstand exposure to chemicals as well as those that are properly cured. Achieving the right temperature ensures that the coating forms a robust, impervious layer that can resist chemical attack. 4.Color and Gloss: Temperature fluctuations can affect the color and gloss of the final finish. Over-curing can lead to discoloration or a loss of gloss, while under-curing may result in a finish that appears uneven or lacks the desired sheen. Optimizing the Curing Process To optimize the curing process, manufacturers must carefully control the temperature and duration of the curing cycle. This can be achieved through the use of advanced curing ovens equipped with precise temperature control systems. Additionally, regular monitoring and calibration of equipment are essential to ensure consistent results. Conclusion The curing temperature is a critical factor in determining the performance and durability of powder coatings. By understanding and controlling this variable, manufacturers can achieve high-quality finishes that meet the stringent demands of various industries. Whether it’s for automotive parts, household appliances, or industrial machinery, getting the curing temperature right is key to ensuring the longevity and aesthetic appeal of powder-coated surfaces. In summary, while powder coatings offer numerous benefits, the curing temperature is the linchpin that determines their ultimate success. By mastering this aspect of the process, companies can enhance the quality and reliability of their coated products, ultimately leading to greater customer satisfaction and improved market competitiveness.
The Impact of Particle Size Distribution on the Performance of Powder Coatings
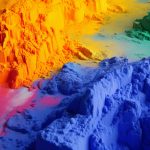
In the world of powder coatings, achieving the perfect finish is a blend of art and science. While the aesthetic and protective qualities of powder coatings are well-documented, one critical factor that significantly influences their performance is often overlooked: particle size distribution. This article delves into how the particle size distribution of powder coatings affects their application, finish quality, and overall performance, providing insights that can help professionals optimize their coating processes. Understanding Particle Size Distribution Particle size distribution (PSD) refers to the range and frequency of different particle sizes in a powder coating. It is typically measured in microns and can vary significantly depending on the manufacturing process and the intended application of the coating. A typical powder coating might have a PSD ranging from 1 to 100 microns, but the majority of particles usually fall within a narrower range. The PSD is crucial because it directly impacts how the powder flows, charges, and adheres during the application process. It also influences the final appearance and durability of the coating. Application Efficiency One of the most immediate effects of PSD is on the application efficiency. Finer particles (typically below 10 microns) are more likely to be overcharged and can lead to issues like “back ionization,” where the powder layer repels incoming particles, resulting in an uneven coating. On the other hand, larger particles (above 70 microns) may not charge efficiently and can lead to poor transfer efficiency, meaning more powder is wasted during application. Optimizing the PSD can significantly enhance transfer efficiency, ensuring that more powder adheres to the substrate and less is lost as overspray. This not only improves the cost-effectiveness of the process but also reduces environmental impact by minimizing waste. Finish Quality The PSD also plays a critical role in determining the finish quality of the coating. A narrow PSD, where most particles are of a similar size, generally results in a smoother, more uniform finish. This is because particles of similar size tend to melt and flow evenly during the curing process, creating a consistent surface. Conversely, a broad PSD with a wide range of particle sizes can lead to a textured finish. While this can be desirable for certain applications, such as those requiring a matte or textured appearance, it can be detrimental for applications requiring a high-gloss, smooth finish. Durability and Performance The durability of a powder coating is influenced by its ability to form a continuous, defect-free film. A well-distributed PSD helps in achieving this by ensuring that particles melt and flow together seamlessly. Finer particles can fill in the gaps between larger particles, resulting in a more cohesive film. Moreover, a balanced PSD can enhance the coating’s resistance to environmental factors such as UV radiation, moisture, and chemicals. This is particularly important for outdoor applications where the coating is exposed to harsh conditions. Optimizing Particle Size Distribution To optimize the PSD for a specific application, manufacturers can employ various techniques, including: 1.Air Classification: This method separates particles based on their size and density, allowing for the production of powders with a more uniform PSD. 2.Milling and Grinding: These processes can be used to reduce the size of larger particles, thereby narrowing the PSD. 3.Blending: Mixing powders with different PSDs can help achieve a desired distribution for specific applications. In conclusion, the particle size distribution of powder coatings is a critical factor that impacts their application, finish quality, and overall performance. By understanding and optimizing the PSD, manufacturers and applicators can achieve superior coating results, enhancing both the aesthetic and protective qualities of the finish. As the demand for high-performance coatings continues to grow, paying attention to PSD will be more important than ever in meeting the needs of diverse applications. By focusing on the nuances of particle size distribution, professionals can unlock the full potential of powder coatings, ensuring that they not only meet but exceed the expectations of their clients.