Archives
now browsing by author
Emerging Technologies Shaping the Future of Powder Coatings
The powder coatings industry is undergoing a transformative phase, driven by technological advancements and the global push toward sustainability. While traditional applications of powder coatings in automotive, construction, and appliance industries are well-documented, the next frontier lies in cutting-edge innovations that redefine performance, efficiency, and environmental impact. This article explores the latest technological breakthroughs and their implications for the future of powder coatings. 1. UV and IR Curing: Revolutionizing Efficiency UV (ultraviolet) and IR (infrared) curing technologies are emerging as game-changersRead More …
The Future of Powder Coatings: Smart and Functional Coatings
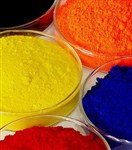
The powder coating industry is undergoing a quiet revolution. While traditional powder coatings have long been valued for their durability, eco-friendliness, and cost-effectiveness, a new generation of smart and functional coatings is pushing the boundaries of what’s possible. These advanced coatings are not just protective layers; they’re transforming surfaces into interactive, intelligent, and multifunctional interfaces. 1. Self-Healing Coatings: The Next Frontier Imagine a world where scratches on your car or appliances disappear on their own. Self-healing powder coatings are makingRead More …
Optimizing Mixed Powder Coatings
Mixed powder coatings are a versatile type of coating created by blending multiple types of powder coatings. They are commonly used to achieve specific color effects, surface textures, or performance characteristics. Below is a concise overview of mixed powder coatings: Composition Mixed powder coatings typically consist of two or more different colored powder coatings. These powders can be of the same type (e.g., epoxy, polyester, acrylic) or different types, depending on the desired performance requirements. Applications Aesthetic Effects: Mixed powder coatings are ideal for achieving special visual effects such as metallic finishes, textured surfaces, or gradient colors. Performance Characteristics: They are also used when specific performance attributes are needed, such as corrosion resistance, wear resistance, or weather resistance. Advantages Versatility: By blending different colors, a wide range of colors and effects can be achieved. Cost-Effectiveness: Mixing existing powders can be more cost-effective than ordering custom colors. Flexibility: The color ratio can be adjusted as needed to achieve different visual outcomes. Disadvantages Consistency: Achieving color consistency can be challenging, especially in large-scale production. Complexity: The mixing process requires precise control to ensure uniform color and performance. Key Application Areas Construction Materials: Such as aluminum profiles, doors, and windows. Automotive Parts: Including wheels and frames. Home Appliances: Like refrigerators and washing machines. Furniture: Such as metal and office furniture. Application Method The application process for mixed powder coatings is similar to that of standard powder coatings, typically using electrostatic spray deposition. It is crucial to ensure the cleanliness of the spray gun and the spraying environment to prevent color contamination. In summary, mixed powder coatings offer a flexible and cost-effective solution for achieving diverse colors and effects. However, careful control and consideration of the mixing process are essential to ensure the desired outcome. Whether for aesthetic or performance reasons, mixed powder coatings can be tailored to meet specific application needs.
Can Powder Coatings Achieve All the Effects of Paint?
When considering the choice between powder coatings and traditional liquid paints, it’s essential to understand the distinct characteristics and capabilities of each. While powder coatings offer numerous advantages and can replicate many effects achieved by paint, there are certain limitations to what they can accomplish. 1. Application Methods and Coating Characteristics Liquid Paints: Application: Liquid paints are applied using methods such as air spray, airless spray, and electrostatic spray. They require solvents and curing agents for proper application and drying. Coating Thickness: Typically, liquid paint coatings are thinner, ranging from 15 to 120 micrometers. Finish Quality: Liquid paints can provide a high gloss and smooth finish, making them ideal for applications where aesthetics are critical, such as automotive surfaces. Powder Coatings: Application: Powder coatings are applied electrostatically and then cured under heat to form a hard, durable finish. Common application methods include electrostatic spray, fluidized bed, and tribo charging. Coating Thickness: Powder coatings generally result in thicker films, typically ranging from 60 to 120 micrometers. Finish Quality: While powder coatings can achieve a variety of finishes, including metallic and textured effects, they may not match the ultra-smooth finish of some liquid paints. 2. Environmental and Safety Considerations Liquid Paints: Environmental Impact: Traditional solvent-based paints contain volatile organic compounds (VOCs) that can be harmful to the environment and human health. Although water-based paints are less harmful, they still require careful handling and disposal. Safety Measures: The use of liquid paints often necessitates strict environmental controls and safety measures to mitigate the risks associated with VOCs. Powder Coatings: Environmental Impact: Powder coatings are solvent-free and emit negligible VOCs, making them an environmentally friendly option. Safety Measures: The application process for powder coatings is generally safer, with no need for stringent environmental controls. 3. Efficiency and Cost Liquid Paints: Application Speed: Liquid paints can be applied quickly, but they often result in higher material waste and require more frequent maintenance. Cost: The initial cost of liquid paint application can be lower, but the need for solvents, curing agents, and environmental controls can increase overall expenses. Powder Coatings: Application Speed: Powder coatings offer faster application and curing times, with less material waste due to the ability to reclaim and reuse overspray. Cost: While the initial investment in powder coating equipment can be higher, the long-term cost benefits, including reduced waste and lower environmental compliance costs, make it a cost-effective option. 4. Applications and Limitations Liquid Paints: Applications: Liquid paints are commonly used in applications where a high-quality finish is crucial, such as automotive finishes, furniture, and artistic applications. Limitations: The environmental impact and safety concerns associated with liquid paints can be a significant drawback in certain applications. Powder Coatings: Applications: Powder coatings are widely used in automotive parts, appliances, metal furniture, and architectural components due to their durability and environmental benefits. Limitations: While powder coatings offer excellent durability and finish quality, they may not be suitable for applications requiring a very thin or ultra-smooth finish. Conclusion In summary, while powder coatings can achieve many of the effects of liquid paints and offer significant advantages in terms of environmental impact, safety, and cost, they may not be able to replicate every effect achievable with liquid paints. The choice between the two depends on the specific requirements of the application, including the desired finish quality, environmental considerations, and budget constraints. Ultimately, both options have their unique strengths and limitations, and the decision should be made based on the particular needs of the project.
Electrostatic powder spraying VS baking paint process
1. Different working methodsElectrostatic spraying mainly uses high-voltage static electricity to adsorb paint particles on the surface of the workpiece; and baking varnish is a new type of spray paint production process. First, the body is polished, then put into the vacuum baking room, sprayed with paint and baked at high temperature.2. Difference in surface:The surface of the object sprayed by electrostatic spraying is relatively smooth, with higher brightness and hardness. The surface of the sprayed paint is matte, withRead More …
Low-Temperature Curing Powder Coatings: A Simplified Guide
Powder coatings are widely used in various industries due to their durability and environmental benefits. However, traditional powder coatings require high-temperature curing, which can be energy-intensive and limit their application on heat-sensitive materials. This is where low-temperature curing powder coatings come into play. What are Low-Temperature Curing Powder Coatings? Low-temperature curing powder coatings are designed to cure at lower temperatures compared to standard powder coatings. This allows for energy savings and expands the range of materials that can be coated. Types of Low-Temperature Curing Powder Coatings 1. Epoxy Powder Coatings: Curing Temperature: 130°C to 160°C Curing Time: 15 to 20 minutes Applications: General industrial use, automotive parts, engine blocks, fuel tanks. 2. Polyester Powder Coatings: Curing Temperature: 140°C to 160°C Curing Time: 15 to 20 minutes Applications: Transportation, automotive frames, heavy machinery, furniture. 3. Epoxy-Polyester Hybrid Powder Coatings: Curing Temperature: 150°C to 160°C Curing Time: 15 to 20 minutes Applications: General industrial use, metal casings, automotive wheel hubs. 4. Acrylic Powder Coatings: Curing Temperature: 150°C to 160°C Curing Time: 15 to 20 minutes Applications: Automotive wheel faces. 5. Matt Powder Coatings: Curing Temperature: 160°C for indoor, 160°C for outdoor (15-20 minutes) Applications: Furniture, appliances, machinery. 6. Interpon Low-E (Low-Temperature) Powder Coatings: Curing Temperature: 30°C lower than standard Applications: Engineering and agricultural machinery, building facades, general industrial use. Advantages of Low-Temperature Curing Powder Coatings 1.Energy Savings: Lower curing temperatures mean reduced energy consumption. For every 10°C reduction in temperature, energy consumption can be reduced by approximately 10%. 2.Expanded ApplicationRead More …
How to Deal with Rust on Powder Coated Surfaces
Powder coating is a popular finish for metal surfaces due to its durability and aesthetic appeal. However, even the most robust powder coatings can fail over time, leading to rust. If you notice rust on your powder coated surfaces, it’s crucial to address the issue promptly to prevent further damage. This guide will walk you through the steps to effectively deal with rust on powder coated surfaces and provide tips to prevent future occurrences. 1. Assess the Damage Before taking any action, it’s essential to evaluate the extent of the rust damage. Minor Rust: If the rust is limited to small areas and hasn’t penetrated deeply, a localized repair might be sufficient. Extensive Rust: If the rust covers large areas or has significantly corroded the metal, a complete recoating might be necessary. 2. Clean the Surface Proper cleaning is crucial to ensure the new coating adheres well. Remove Rust: Use a wire brush, sandpaper, or an electric sander to eliminate rust from the affected areas. Ensure all loose rust and old coating are thoroughly removed. Clean Thoroughly: Use a degreaser and water to clean the surface, removing any oil, dirt, or other contaminants. A clean surface is essential for the new coating to adhere properly. 3. Sand the Surface Sanding helps to smooth out the surface and improves the adhesion of the new coating. Sand the Area: Use medium to fine-grit sandpaper to sand the rusted areas. This will create a smooth surface for the new coating. Ensure Evenness: Make sure the sanded area is even and free of bumps or irregularities. 4. Apply a Rust-Inhibitive Primer A good quality primer is essential to prevent future rusting. Choose the Right Primer: Select a rust-inhibitive primer suitable for metal surfaces. Epoxy primers are often recommended for their excellent rust-preventing properties. Apply the Primer: Follow the manufacturer‘s instructions to apply the primer. Typically, two coats are recommended, allowing sufficient drying time between each coat. 5. Reapply Powder Coating Once the primer is dry, you can proceed to reapply the powder coating. Select the Right Powder Coating: Choose a powder coating that matches the original or opt for one with enhanced corrosion resistance. Apply the Powder Coating: Use an electrostatic spray gun to apply the powder coating evenly. Ensure the coating thickness is consistent. Cure the Coating: Follow the manufacturer’s guidelines to cure the coating. This usually involves baking the coated item at a specific temperature to ensure the coating is fully cured. 6. Inspect and Maintain After the coating has cured, inspect the surface for any defects such as bubbles or peeling. Inspect the Coating: Check for any imperfections and address them promptly. Regular Maintenance: Regularly inspect the coated surfaces and perform any necessary maintenance to extend the life of the coating. Preventive Measures Choose High-Quality Powder Coating: High-quality coatings generally offer better corrosion resistance. Ensure Proper Surface Preparation: Thorough surface preparation is key to ensuring good adhesion and durability of the coating. Regular Inspections: Conduct regular inspections to catch any potential issues early and address them before they escalate. By following these steps, you can effectively deal with rust on powder coated surfaces and prevent future occurrences. Proper maintenance and timely repairs are essential to ensure the longevity and appearance of your powder coated items.
Thermoplastic vs. Thermosetting Powder Coatings: Choosing the Right Option
When selecting a powder coating for your project, understanding the differences between thermoplastic and thermosetting powder coatings is crucial. Each type offers unique properties and advantages, making them suitable for different applications. Below, we break down their key differences and provide guidance on selecting the right coating for your needs. Thermoplastic Powder Coatings Definition & Characteristics: Thermoplastic powder coatings are made from thermoplastic resins that melt when heated and solidify upon cooling without undergoing any chemical change. These coatings have high molecular weight and offer excellent flexibility but are challenging to grind into fine particles and exhibit poor flow during baking. Advantages: Simple processing and application: They only require heating, melting, flowing, and cooling or extraction to form a film, eliminating the need for complex curing equipment. Superior chemical resistance, water resistance, and wear resistance. Disadvantages: High melting temperatures and lower colorability compared to thermosets. Poor adhesion to metal surfaces and less desirable film appearance. Applications: Commonly used in pipelines, mechanical bearings, printer components, mechanical gears, and textile equipment. Examples: Polyethylene coatings for highway and railway fences; PVC coatings for household appliances and metal mesh products. Thermosetting Powder Coatings Definition & Characteristics: Thermosetting powder coatings use thermosetting resins that, upon heating, undergo a chemical reaction (cross-linking) to form an insoluble and infusible film. These resins have lower molecular weight, allowing for better flow and enhanced decorative properties. Advantages: Superior mechanical properties and corrosion resistance due to the formation of a cross-linked network structure. Better film appearance and can meet high-performance requirements. Disadvantages: More complex processing and application: They require specialized curing equipment. Applications: Widely used in household appliances, transportation, construction materials, industrial equipment, plastics, and powder metallurgy. Examples: Epoxy coatings for high-protection applications; polyester coatings for indoor and outdoor use. Choosing the Right Coating 1. Application Environment: Thermosets are ideal for high-temperature or harsh environments due to their superior corrosion resistance and mechanical properties. Thermoplastics are suitable for applications requiring high chemical and solvent resistance. 2. Cost Considerations: Thermoplastics generally have lower costs and simpler processing, making them a cost-effective choice for budget-conscious projects. Thermosets are more expensive but offer superior performance, making them suitable for high-end applications. 3. Film Appearance & Performance Requirements: Thermosets are preferred when high film appearance and flow are required. Thermoplastics are suitable when high chemical resistance and wear resistance are needed.
Zinc-Rich Paint: Types and Applications
Zinc-rich paint is a specialized type of anti-corrosion coating widely used in industrial and construction settings. It primarily relies on zinc particles to provide cathodic protection, effectively preventing steel corrosion. Here’s a simplified overview of the different types of zinc-rich paint and their typical applications. Types of Zinc-Rich Paint 1. Epoxy Zinc-Rich Primer Composition: Contains high levels of zinc powder mixed with epoxy resin and a hardener. Characteristics: Excellent adhesion, abrasion resistance, and chemical resistance. Dries quickly and is easy to apply. Provides strong cathodic protection. Applications: Ideal for protecting steel structures such as bridges, ships, and storage tanks. Widely used in industrial environments where corrosion resistance is crucial. 2. Inorganic Zinc-Rich Primer Composition: Made with inorganic silicates (like potassium silicate) and zinc powder. Characteristics: Superior heat resistance, solvent resistance, and chemical resistance. Hard film with good electrical conductivity. Suitable for high-temperature and harsh environments. Applications: Commonly used for the exterior of high-temperature pipes and the interior of storage tanks. Ideal for marine environments and other harsh conditions. 3. Waterborne Inorganic Zinc-Rich Primer Composition: Consists of water-based silicate solutions and zinc powder. Characteristics: Environmentally friendly with low VOC content. Safer to apply as it is non-flammable. Versatile in various application environments. Applications: Suitable for steel structure protection, especially in environments where environmental safety is a concern, such as bridges and port facilities. 4. Solvent-Based Inorganic Zinc-Rich Primer Composition: Contains alkyl silicates and zinc powder. Characteristics: Dries rapidly and forms a hard film. Requires careful surface preparation of the steel. Applications: Used for steel protection in atmospheric conditions. Zinc-rich paints are valued for their exceptional corrosion resistance and versatility. The choice of zinc-rich paint type depends on the specific application environment and requirements. Inorganic zinc-rich paints are best for high-temperature and harsh conditions, while epoxy zinc-rich paints are more suitable for general industrial and construction applications. Waterborne inorganic zinc-rich paints offer environmental and safety benefits, making them ideal for projects with strict environmental regulations.
Alkyd Paint: An Overview
Alkyd paint, also known as alkyd resin paint, is a versatile synthetic resin coating widely used in various applications. It is one of the most popular and cost-effective paint options available today. Composition Alkyd Resin: The primary component, derived from polyhydric alcohols (like glycerol) and polybasic acids (such as phthalic anhydride), often combined with oils or fatty acids. Pigments: Provide color and opacity. Solvents: Used to adjust viscosity and drying time, commonly including mineral spirits and xylene. Additives: Enhance properties like UV resistance and durability. Key Features and Benefits Durability: Alkyd paint forms a tough, protective layer that withstands wear and weathering, making it ideal for both indoor and outdoor use. Versatility: Offers different finishes, including high gloss, semi-gloss, and matte, catering to various aesthetic needs. Ease of Application: It has excellent flow and adhesion properties, making it easy to apply on multiple surfaces like wood, metal, and more. Quick Drying: Dries relatively fast, which speeds up the painting process. Weather Resistance: Exhibits good resistance to weathering, making it suitable for exterior applications. Applications Decorative and Protective: Commonly used for painting furniture, doors, windows, and metal surfaces in residential and commercial settings. Industrial Uses: Suitable for general metal protection in industries such as automotive, agriculture, and machinery. Environmental Considerations VOC Content: Traditional alkyd paints contain volatile organic compounds (VOCs), which can affect indoor air quality. Proper ventilation is recommended during application. Eco-friendly Options: Water-based alkyd paints are gaining popularity due to their lower VOC content and reduced environmental impact. Conclusion Alkyd paint remains a popular choice for many due to its affordability, ease of use, and durability. It is ideal for a wide range of applications, from household items to industrial equipment. However, when choosing alkyd paint, consider the specific needs of your project and the environmental impact, and opt for water-based variants if sustainability is a priority.