Archives
now browsing by author
Waterborne Polyurethane Coatings vs. Polyurethane Powder Coatings
1. Substrate Compatibility Waterborne Polyurethane Coatings: Suitable for a variety of substrates, including wood, metal, plastic, and concrete. Particularly effective on wood and plastic due to excellent adhesion properties. Polyurethane Powder Coatings: Primarily used on metal surfaces such as steel and aluminum. Offers superior adhesion and protection for metal substrates but is less effective on non-metallic materials. 2. Application Methods Waterborne Polyurethane Coatings: Applied using wet methods such as spraying, brushing, or rolling. Requires controlled humidity and temperature conditions for optimal application. Polyurethane Powder Coatings: Applied using dry methods like electrostatic spraying or fluidized bed dipping. Requires a curing process at high temperatures, making it more complex. 3. Performance Characteristics Waterborne Polyurethane Coatings: Wear and Chemical Resistance: Excellent. Flexibility: High, making it ideal for applications requiring elasticity. Water Resistance: Good, though special treatments may be needed for long-term immersion. Polyurethane Powder Coatings: Wear and Impact Resistance: Superior. Chemical Corrosion Resistance: Strong. Weather Resistance: High, suitable for outdoor environments. 4. Environmental Impact Waterborne Polyurethane Coatings: Environmentally friendly with low VOC content. Non-flammable and odorless, posing minimal health risks. Polyurethane Powder Coatings: Completely free of solvents, resulting in zero VOC emissions. No waste gases are produced during application, making it highly eco-friendly. 5. Color Selection Waterborne Polyurethane Coatings: Offers a wide range of colors and gloss levels. Colors are vibrant and can achieve high decorative effects. Polyurethane Powder Coatings: Available in multiple colors but with a narrower selection compared to waterborne coatings. Colors are uniform, though gloss level adjustments are less flexible. 6. Applications Waterborne Polyurethane Coatings: Ideal for wood furniture, building interiors/exteriors, automotive interiors, and corrosion protection. Polyurethane Powder Coatings:Read More …
The Environmental Impact of Low-Temperature Powder Coatings
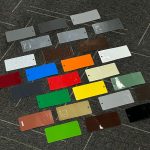
In the ever-evolving world of industrial coatings, powder coatings have gained significant traction due to their durability, efficiency, and environmental benefits. While the industry often focuses on the broader advantages of powder coatings, such as their lack of volatile organic compounds (VOCs) and reduced waste, a niche area that deserves more attention is the development and impact of low-temperature powder coatings. This article delves into the unique benefits and environmental implications of these innovative coatings. What are Low-Temperature Powder Coatings?TraditionalRead More …
Metal Brushing: An Overview of the Process, Types, and Applications
Metal brushing is a widely used surface treatment technique in various industries, primarily for decorative and functional purposes. This process involves creating fine lines or textures on metal surfaces through mechanical or chemical means, enhancing both the aesthetic appeal and durability of the material. This article provides a comprehensive overview of metal brushing, including its principles, types, applications, and benefits. 1. Process Principles Basic Concept: Metal brushing alters the surface of metal by creating fine lines or textures. This is achieved through mechanical grinding or chemical treatments, resulting in a matte or brushed finish. The process not only enhances the visual appeal but also improves the surface’s resistance to wear and corrosion. Key Steps: Degreasing: The metal surface is first cleaned to remove oils, dirt, and other impurities. This step is crucial for ensuring a smooth and consistent finish. Grinding: The surface is then abraded using tools such as sandpaper, sanding belts, or brushes. This step creates the desired texture and pattern on the metal. Washing: After grinding, the surface is thoroughly washed to remove any residues from the brushing process. 2. Types of Brushing Straight Line Brushing: This method involves creating parallel lines on the metal surface using mechanical friction. It is commonly used for decorative purposes and to conceal surface scratches. Random Brushing: Unlike straight line brushing, random brushing produces a more natural, less uniform texture. This type of finish is often used when a more refined and less patterned look is desired. Circular Brushing: This technique uses a rotating tool to create circular or spiral patterns on the metal surface. It is often employed for decorative applications where a unique texture is required. 3. Applications Metal brushing is utilized across a range of industries due to its versatility and effectiveness in enhancing metal surfaces: Electronics: The exterior casings of devices such as smartphones and laptops frequently undergo metal brushing to improve their aesthetic appeal and provide a premium feel. Home Appliances: Products like ovens and rice cookers often feature brushed metal finishes, which not only enhance their appearance but also increase their durability. Automotive Industry: While not as prevalent as in other sectors, metal brushing is still used in automotive interiors to add a touch of elegance and sophistication. 4. Advantages Decorative Appeal: Metal brushing significantly enhances the visual appeal of metal surfaces, making them more attractive and modern. Functionality: The process can conceal manufacturing defects and mechanical marks, while also providing a degree of corrosion resistance. Durability: Brushed metal surfaces are often more resistant to scratches and wear, making them suitable for high-traffic areas and products that require long-term durability. 5. Common Materials Aluminum: Known for its lightweight and corrosion-resistant properties, aluminum is a popular choice for metal brushing, especially in the electronics and automotive industries. Stainless Steel: Widely used in appliances and architectural applications, stainless steel benefits from the added durability and aesthetic enhancement provided by brushing. Copper: With its distinctive color and excellent conductivity, copper is often brushed for decorative applications in art and design. Conclusion Metal brushing is a versatile and effective technique that enhances both the appearance and functionality of metal surfaces. By understanding the different types of brushing and the materials they can be applied to, manufacturers and designers can create products that are not only visually appealing but also durable and functional. Whether in electronics, home appliances, or automotive interiors, metal brushing continues to be a valuable process in modern manufacturing.
JINHU Color Powder Coating Co. Ltd. Achieves Additional Qualicoat Certifications
In a significant milestone for JINHU Color Powder Coating Co. Ltd., we are thrilled to announce that our range of powder coatings has successfully passed additional Qualicoat certifications. This achievement underscores our commitment to quality, innovation, and meeting the evolving needs of our global clientele. A Testament to Quality and Excellence Qualicoat is a globally recognized standard for excellence in the coating industry, known for its rigorous testing and high-quality benchmarks. The recent certification of more colors in our powder coating line is a testament to our dedication to maintaining the highest standards of quality and performance. Broadening Our Color Spectrum The newly certified colors include a variety of shades that cater to diverse aesthetic preferences and functional requirements. From the deep, rich tones of RAL 3005 to the classic elegance of RAL 9010, our expanded palette offers more choices for architects, designers, and manufacturers seeking durable and vibrant finishes. Unwavering Commitment to Innovation At JINHU, innovation is at the heart of what we do. The additional Qualicoat certifications reflect our continuous efforts to push the boundaries of what’s possible in powder coating technology. Our R&D team has worked tirelessly to develop coatings that not only meet but exceed industry standards, ensuring that our products deliver exceptional performance in various environmental conditions. Benefits to Our Valued Clients The expanded range of Qualicoat-certified colors brings several advantages to our clients: Enhanced Durability: Our coatings are designed to withstand harsh weather conditions, ensuring long-lasting protection and aesthetic appeal. Environmental Responsibility: Qualicoat certification also means our products meet strict environmental regulations, aligning with global sustainability goals. Versatility: With a broader spectrum of colors, our clients can achieve the perfect look for their projects, whether it’s for architectural applications, automotive finishes, or industrial equipment. Looking Ahead As we celebrate this achievement, we remain committed to further expanding our product offerings and enhancing our technological capabilities. Our goal is to continue providing our clients with high-quality, innovative solutions that meet the highest international standards. Join Us in Celebrating This Milestone We invite our partners, clients, and industry peers to join us in celebrating this significant milestone. The additional Qualicoat certifications are not just a mark of quality but a promise of excellence that we extend to all our stakeholders. For more information about our Qualicoat-certified powder coatings and to explore our expanded color range, please visit our website or contact our sales team. About JINHU Color Powder Coating Co. Ltd. JINHU Color Powder Coating Co. Ltd. is a leading manufacturer of high-quality powder coatings. With a strong commitment to innovation, quality, and customer satisfaction, we provide a wide range of coating solutions for various industries worldwide. Our state-of-the-art facilities and dedicated team ensure that we meet the highest standards of excellence in every product we deliver.
Coatings professional terminology explanation
Q: What is environmentally friendly paint?A: Generally, environmentally friendly paints that do not emit VOC or strictly limit the emission to below the specified indicators, such as water-based paints, high-solid paints, powder paints and radiation-cured paints, are called “green paints” or environmentally friendly paints. Q: What is powder paint?A: Powder paint is a new type of solvent-free, 100% solid powder paint. It has two types: thermoplastic powder paint and thermosetting powder paint. The paint is made of special resins, pigments,Read More …
Exploring the Versatile World of Powder Coating Application Methods
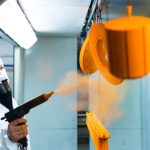
Powder coating has revolutionized the finishing industry with its eco-friendly, durable, and cost-effective solutions. Unlike traditional liquid coatings, powder coatings do not contain solvents, reducing the emission of volatile organic compounds (VOCs) and contributing to a greener planet. The application of powder coatings is a critical step in achieving the desired finish, and several methods are employed to cater to various industrial needs. This article delves into the primary powder coating application techniques, highlighting their unique features and applications. StaticRead More …
Powder paint spraying cases
Recently, we visited our largest customer in Ukraine, who has been using our powder coatings for many years.Usually, they use our powder coatings on shelves, express cabinets, display cabinets, cash register systems, etc.
Comparative Analysis of Surface Treatment Methods for Aluminum Profiles: Powder Coating vs. Painting vs. Anodizing
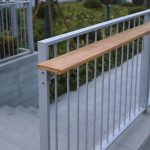
Introduction The selection of surface treatment methods for aluminum profiles significantly impacts the aesthetics, durability, and functionality of the final product. Among the popular choices, powder coating stands out for its environmental benefits, durability, and versatility. This article delves into a detailed comparison of powder coating with traditional painting and anodizing methods. Powder Coating vs. Painting Environmental Benefits and Safety:Powder coating is a dry finishing process that emits minimal volatile organic compounds (VOCs), making it a more environmentally friendly optionRead More …
The Versatile World of Anti-Popping Powder Coatings
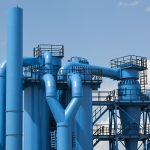
In the realm of industrial coatings, anti-popping powder coatings have emerged as a game-changer, offering a superior solution for achieving flawless finishes with minimal defects. These specialized coatings are meticulously engineered to prevent or significantly reduce the formation of bubbles and pinholes during the curing process, ensuring a smooth and durable finish across a wide range of applications. Key Applications of Anti-Popping Powder Coatings 1.Architectural Aluminum Extrusions: With their exceptional weather resistance and aesthetic appeal, anti-popping powder coatings are widelyRead More …