Chemical surface preparation before powder coating
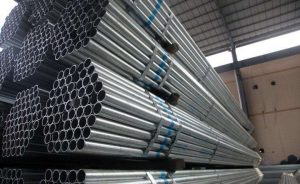
Particular application is closely related to the nature of the surface being cleaned and the nature of the contamination. Most surfaces powder coated after cleaning are either galvanized steel, steel, or aluminum. Since not all chemical-type preparations are applicable to all these materials, the preparation process selected depends on the substrate material. For each material, the type of cleaning will be discussed and its unique features for that substrate will be explained. Specific application processes are quite similar for each material.
CLEANING GALVANIZED STEEL
Alkaline Cleaners
Alkaline cleaners for galvanized steel usually have a blend of mild alkaline salts that do not damage the zinc surface. In some cases, a small-to-moderate amount of free caustic soda may be present in the cleaner to remove difficult soils or to provide a desired etch. These cleaners can be applied by power spray, immersion, electrocleaning, or hand wipe.
In the power spray method, the parts to be cleaned are suspended in a tunnel while the cleaning solution is pumped from a holding tank and sprayed, under pressure, onto the parts. The cleaning solution then is continuously recirculated. Spray pressure ranges from 4 to 40 psi.
In the immersion method, parts to be cleaned are simply immersed in a solution of the cleaner contained in a mild steel or stainless steel tank.
Electrocleaning is a specialized version of immersion cleaning in which a direct current is passed through the solution. The parts to be cleaned are hung in the solution and are the anode, while other electrodes act as the cathode. Electrocleaning is more effective than plain immersion due to the scrubbing action of the gas bubbles produced at the surface of the part.
The hand-wiping method of application derives additional benefit from the physical act of removing the soil from the surface by means of a cloth or sponge, with the cleaner helping to solubilize the soils.
Alkaline cleaners are usually applied to galvanized zinc surfaces in two stages-the cleaning stage and a water rinse stage. The parts to be cleaned are usually conveyed from one stage to the other after suitable exposure to produce cleaning. Additional stages of cleaning and rinsing may be used if required. The chemicals in the baths for this type are usually maintained at a temperature between 80 and 200°F (27 and 93°C). Typically the temperature is 120 to 150°F (49 to 66°C) for spray and 150°F (66°C) for immersion. The time for which the parts are exposed to these chemicals is between 30 seconds and 5+ minutes. Generally, it is 1 to 2 minutes for spray and 2 to 5 minutes for immersion. To be effective, the concentration of such alkaline cleaning solutions should be between 1/4 and 16 odgal(2 to 120 g/ L). Typically, in the spray the concentration is 1/2 to 1 odgal(4 to 8 g/L) and for immersion 6 to 12 odgal(45 to 90 g/L).
The most expensive of these types is the electrocleaner, due to the higher bath concentrations used and the cost of electricity for the electrocleaner. The least expensive is the spray cleaner, with hand-wiping somewhere in between. The alkaline type is, by far, the most effective and usually the least expensive to operate. In order of decreasing performance, the methods of application would generally be rated as: electrocleaning, spray cleaning, immersion cleaning, and hand wiping.
Acid Cleaners
Acid cleaners are not normally used to clean galvanized steel. Of those acid cleaners that are used, the most common type would be mildly acidic salts, not too corrosive to the zinc surface. It should be noted, however, that there are specialty acid cleaners designed to remove white corrosion product from galvanized surfaces.
In the power spray method of application, the parts to be cleaned are suspended in a tunnel while the cleaning solution is pumped from a holding tank and sprayed under pressure onto the parts. The cleaning solution then is drained back into the holding tank and the cycle repeated. The pumping, spraying, and draining operations take place simultaneously and continuously.
When the immersion method of application is used, the parts to be cleaned are simply immersed in a solution of the cleaner contained in a mild steel or stainless steel tank.
Electrocleaning with acid cleaners is a specialized version of immersion cleaning in which a direct current is passed through the solution. The parts to be cleaned are usually the anode, while other electrodes act as the cathode. Electrocleaning usually produces a cleaner surface than plain immersion due to the scrubbing action of the oxygen bubbles coming off at the surface of the part. The oxygen is a result of the electrolysis of the water.
The hand-wiping method derives additional benefit from the mechanical aid of physically moving the soil from the surface by means of a cloth or sponge with the cleaner helping to solubilize the soils.
Acid cleaners are usually applied to galvanized zinc surfaces in two stages: the cleaning stage and a water rinse. Additional stages, cleaning and rinsing, may be used if required. The chemicals in the bath are maintained at a temperature of 80 to 200°F (27 to 93°C);typically 100 to 140°F (38 to 60°C) for spray and 140 to 180°F (60 to 82°C) for immersion. The parts are exposed to the chemicals for 30 seconds to 5+ minutes; typically 1 to 2 minutes for spray and 2 to 5 minutes for immersion. The solutions are kept at a concentration of 1/4 to 16 odgal(2 to 120 gL); typically 1/2 to 1 odgal(4 to 8 gL) for spray and 4 to 12 odgal(30 to 90 g/L) for immersion.
In order of decreasing performance, the methods of application would generally be rated as: electrocleaning, spray cleaning, immersion cleaning, and hand-wiping.
Neutral Cleaners
A neutral cleaner (as used for galvanized steel) may be composed of surfactants only, neutral salts plus surfactants, or surfactants with other organic additives. A neutral cleaner may be defined as any cleaner which, in solution, would register between 6 and 8 on the pH scale.
With the power spray method, parts to be cleaned are suspended in a tunnel while the cleaning solution is pumped out of a holding tank and sprayed, under pressure, onto the parts. The cleaning solution is continuously recirculated. Spray pressure ranges from 4 to 40 psi.
In the immersion method of application, the parts to be cleaned are simply immersed in a solution of the cleaner contained in a mild steel or stainless steel tank.
Once again, hand-wiping has an additional benefit from the mechanical aid of physically moving the soil from the surface by means of a cloth or sponge, with the cleaner helping to solubilize the soils.
Neutral cleaners are usually applied by using a minimum of two stages: the cleaning stage and a water rinse. Additional stages, a cleaning and rinsing, may be used if required. The solutions are held at a temperature of 80 to 200°F (26 to 93°C); typically 120 to 160°F (49 to 71°C) for spray and 150 to 180°F (66 to 82°C) for immersion. The parts are exposed for 30 seconds to 5+ minutes; typically 1 to 2 minutes for spray and 2 to 5 minutes for immersion.
The solutions are held at a concentration of 1/4 to 16 odgal(2 to 120 gL); typically 1 to 2 odgal(8 to 16 gL) for spray and 8 to 14 odgal(60 to 105 g/L) for immersion. Neutral cleaners are not effective as the primary cleaner. They are more likely to be used as a precleaner.
Comments are Closed