Common Problems and Solutions in Powder Coating Application
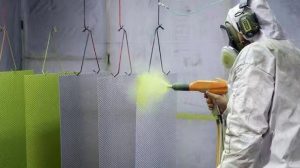
Powder coating is a widely used method for providing durable and attractive finishes on various substrates. However, during the application process, certain issues can arise, affecting the quality of the coated film. Understanding and effectively troubleshooting these common problems is essential for achieving desired results. In this article, we will explore solutions to common issues such as insufficient gloss, discoloration, orange peel texture, pinholes, and air bubbles in powder coatings.
Insufficient Gloss:
- Curing time: Ensure the baking time is appropriate, avoiding excessive heating that can result in diminished gloss.
- Temperature control: Maintain optimal oven temperature to prevent excessive heat, which may affect glossiness.
- Gas contamination: Ensure a clean and controlled environment in the oven, free from contaminants that can affect gloss.
- Surface preparation: Adequately prepare the work surface, ensuring it is smooth and free from imperfections that can impact gloss.
- Proper pre-treatment: Select an appropriate pre-treatment method to enhance adhesion and glossiness.
Discoloration:
- Excessive baking cycles: Minimize repeated baking cycles, as it can lead to discoloration of the powder coating.
- Gas contamination: Ensure the oven is free from gases or contaminants that can cause discoloration.
- Over-baking during curing: Control the curing temperature and time to prevent discoloration.
- Excessive coating thickness: Apply the powder coating within the recommended thickness to avoid discoloration.
Orange Peel Texture:
- Uneven coating thickness: Apply the powder coating uniformly to achieve a consistent texture.
- Proper powder atomization: Ensure optimal powder spraying, avoiding powder accumulation and resulting orange peel texture.
- Curing temperature: Adjust the curing temperature as per the powder coating manufacturer’s recommendations to achieve the desired texture.
- Powder quality: Store the powder properly to prevent moisture absorption, which can lead to coarse particles and orange peel texture.
- Good grounding: Maintain a proper grounding connection to avoid irregularities in the coating texture.
- Baking temperature control: Ensure the oven temperature is within the specified range, avoiding excessively high temperatures that can result in orange peel texture.
- Inadequate coating thickness: Apply the powder coating with an appropriate thickness to achieve the desired texture and appearance.
Pinholes:
- Surface preparation: Thoroughly clean and properly remove oil and impurities from the surface to prevent pinhole formation.
- Air source cleanliness: Ensure the compressed air used for spraying is properly filtered, eliminating oil and water contaminants.
- Surface irregularities: Prepare the surface properly to achieve a smooth and even base, preventing pinholes.
- Equipment cleanliness: Keep the spraying equipment clean to prevent dust and impurities from contaminating the powder coating process.
Air Bubbles:
- Surface drying: Ensure the surface is completely dry after pre-treatment, preventing residual moisture that can result in air bubbles.
- Adequate degreasing and rust removal: Thoroughly remove grease and rust from the surface to prevent air bubble formation.
- Volatile component evaporation: Ensure complete evaporation of volatile components in the base layer before applying the powder coating.
- Surface porosity: Address surface imperfections and porous spots on the substrate that may result in air bubble formation.
- Controlled coating thickness: Apply the powder coating with the recommended thickness to minimize the risk of air entrapment and bubble formation.
Powder coating application can encounter common issues such as insufficient gloss, discoloration, orange peel texture, pinholes, and air bubbles. By implementing the recommended solutions, including proper temperature control, surface preparation, powder application techniques, and cleanliness, these problems can be effectively troubleshooted. Achieving high-quality powder coatings requires attention to detail and adherence to best practices during the application process, resulting in durable and visually appealing finishes across various industries and applications.