Early Silicon-Based Technologies in high temperature powder coating
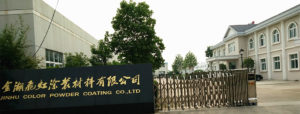
Silicon resins have been used in high-performance liquid coatings for more than 40 years, including applications such as exhaust stacks, boilers, engines, mufflers and heat exchangers. When SBTs first started gaining commercial acceptance in the powder coatings market during the early 1990s, many powder-coating resins were materials based on formulations originally designed for liquid deposition.
In today’s market, however, there are silicone-based resins designed specifically for powder coatings. Commercial formulations are generally either phenyl- or methyl-based, and are used to improve thermal properties and UV performance of heat- and weather-resistant powder coatings. Their performance can be attributed to several chemical phenomena, including the following.
- Stability of the silicon-oxygen-silicon bond (Si-O-Si), as evidenced by its abundance in nature in quartz rock, sand and other minerals.
- Stability of organic radicals attached to the silicon atom, a result of the screening effect of the siloxane bond.
- Formation of stable Si-O-Si bonds within the polymer upon partial disintegration (in contrast to organics, which progressively deteriorate).
- Insulating effect of the siloxane layer formed during thermal oxidation.
Although they delivered good performance in high-heat applications, the first generation of methyl-based products created compatibility issues for powder-coating producers. This was due to the potential for cross-contamination when processing silicon-containing formulations and organics on the same equipment. The problem can also arise from the presence of materials such as polydimethylsiloxane fluid, which help improve flow, leveling and mar resistance when used at appropriate molecular weights and concentrations, but can result in adhesion loss or cratering at excessive levels.
Increased phenyl content will improve the organic compatibility of a silicon-based resin. When combining different resin chemistries, good compatibility ensures intimate blending, without which the resin blends can establish distinct SBT/organic domains. The boundary layers of these domains are weak links in the resin matrix and detract from the physical properties of the film. Further, even though a particular formulation contains only one resin, the processing and application equipment will invariably handle other materials. Like many acrylics, silicone resins require special attention to avoid cross-contamination of dissimilar powder systems.
Extreme Temperature Service
In any powder-coating formulation, extreme temperatures (>1,000 degrees F) cause all of the organic components to oxidize. This leaves only the residual matrix of silicon dioxide bonded to the inorganic pigments and fillers to comprise the coating film.
Early resin systems based on all-phenyl silicones displayed better organic compatibility, but had performance limitations, especially at higher temperatures. When the organic components oxidize completely, high-phenyl resins will exhibit a greater weight loss than that of a methyl-based resin, which affects film integrity and thermal stability.
As such, silicone resins with lower phenyl-to-methyl ratios (and subsequently higher residual silicon dioxide content) are likely to possess better thermal properties.
Manufacturing and Cure Mechanism
Silicone resins for powder coatings are synthesized in solvent, then stripped and flaked. When used in traditional solvent-based liquid coatings, residual solvent in the flake resin is not an issue. In powder-coating applications, however, effective solvent removal is crucial in avoiding surface defect problems, process odors and sintering of the coating. Strict process control during manufacturing is needed to ensure that no significant amount of residual solvent remains in the flaked resin.
Another key property in a silicone resin is the crosslink density, or the degree of substitution. Atomic silicon has four valence sites, which bond with four oxygen atoms. The manufacturing process for silicone-based resin formulations involves substituting one or more of these oxygen atoms (usually with phenyl and/or methyl) by way of chemical reaction.
The number of substituted oxygen atoms per silicon atom is referred to as the degree of substitution, which determines a commercial resin’s physical form between a hard, brittle solid and a low-viscosity fluid. Formulators can vary the form of their finished product by selecting a material with the appropriate crosslink density.
Comments are Closed