Factors affecting measurement uncertainty -ISO 2360
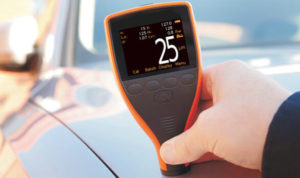
Measurement of coating thickness
INTERNATIONAL STANDARD
ISO 2360
5 Factors affecting measurement uncertainty
5.1 Coating thickness
A measurement uncertainty is inherent in the method. For thin coatings, this measurement uncertainty (in absolute terms) is constant, independent of the coating thickness and, for a single measurement, is at least 0,5μm. For coatings thicker than 25 μm, the uncertainty becomes relative to the thickness and is approximately a constant fraction of that thickness.
For measuring coating thicknesses of 5 μm or less, the average of several measurements shall be taken.
It may not be possible to obtain the measurement uncertainty specified in Clause 8 when measuring coatings of less than 3 μm in thickness.
5.2 Electrical properties of the basis materials
Measurements using eddy current instruments can be affected by the electrical conductivity of the basis metal, which is a function of the composition and heat treatment of the material. The influence of electrical conductivity on the measurement varies considerably with the make and type of instrument.
5.3 Basis metal thickness
For each instrument there is a critical minimum basis metal thickness above which measurements are not affected by an increase in thickness. Since this thickness depends on both the eddy current generation frequency of the probe system and the electrical properties of the basis material its value should be determined experimentally, unless otherwise specified by the manufacturer.
An explanation of Eddy current generation and the calculation of the required minimum basis materia thickness, dmin, is given in Annex A.
However, in the absence of any other information, the required minimum basis material thickness, dmin, can be estimated from the equation:
dmin = 2,5 δ0
where δ0 is the standard penetration depth of the basis material (see A.1).
5.4 Edge effects
Eddy current instruments can be sensitive to abrupt changes in surface contour of test specimen. Therefore measurements made too near to an edge or corner may not be valid unless the instrument has been specifically calibrated for such measurements (see 6.2.4 and Annex B).
NOTE When compared with the phase-sensitive method of ISO 21968, the amplitude-sensitive eddy current instruments can be substantially more heavily affected by edge effects.
5.5 Surface curvature
Measurements are affected by the curvature of the test specimen. This influence of curvature varies considerably with the make and type of instrument and probe, but always becomes more pronounced as the radius of curvature decreases. Measurements made on curved test specimens might not, therefore, be valid unless the instrument is specifically calibrated for the surface curvature in question, or a special probe, which compensates for surface influence, is used.
5.6 Surface roughness
Measurements are influenced by the surface topography of the basis material and of the coating. Rough surfaces can cause both systematic and random errors. Random errors can be reduced by making multiple measurements, each measurement being made at a different location, and then calculating the average value of that series of measurements.
If the basis material is rough, the zero of the instrument shall be checked at several locations on a typical sample of the uncoated, rough, basis material. If no typical uncoated basis material is available, the coating of the test specimen shall be stripped, at least over part of its area, with a chemical solution that does not attack the basis material.
NOTE When compared with the phase-sensitive method of ISO 21968, the amplitude-sensitive eddy current measurement can be more heavily affected by basis material roughness.
5.7 Lift-off effect
If the probe is not placed directly on the coating, the gap between probe and coating (“lift-off”) affects the measurement of the coating thickness. The measured thickness will be equal to the coating thickness plus the additional “lift-off” gap.
Lift-off can be produced unintentionally, e.g., by the presence of foreign particles between the probe and the coating.
The probe tip shall be checked frequently for cleanliness.
5.8 Probe pressure
The pressure with which the probe is applied to the test specimen affects the instrument readings and shall therefore be made constant.
This pressure effect is more noticeable when the coatings are soft. Most commercially-available instruments are supplied with constant pressure probes.
5.9 Probe tilt
Unless otherwise instructed by the manufacturer, the probe shall be applied perpendicularly to the coating surface as tilting the probe away from the perpendicular can cause measurement errors.
The possibility of tilt occurring inadvertently can be minimized by probe design or by the use of a probe-holding jig.
5.10 Temperature effects
Because temperature changes affect the characteristics of the probe, it should be used under approximately the same temperature conditions as those used for calibration unless the probe has built-in temperature compensation.
5.11 Intermediate coatings
The presence of an intermediate coating can affect the measurement of the coating thickness if the electrical characteristics of that intermediate coating differ from that of the coating or basis material. If a difference does exist then the measurements will, in addition, be affected by an intermediate coating thickness of less than dmin. If the thickness is greater than dmin then the intermediate coating, if non-magnetic, can be treated as the basis material.
It has been found that some instruments having probe systems operating with multiple frequencies can measure both top and intermediate coatings.
Comments are Closed