Factors affecting the leveling property of powder coatings
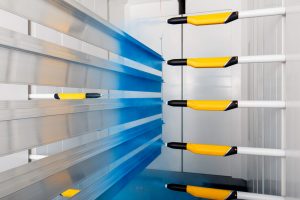
Powder coating is a new type of solvent-free 100% solid powder coating. It has two main categories: thermoplastic powder coatings and thermosetting powder coatings. The paint is made of resin, pigment, filler, curing agent and other auxiliaries, mixed in a certain proportion, and then prepared by hot extrusion and sifting and sieving. They are stored at room temperature, stable, electrostatic spraying or fluidized bed dip coating, reheating and baking melt solidification, so that the formation of a smooth and long-lasting coating film, to achieve the purpose of decoration and corrosion protection.
The so-called leveling of the paint means that the paint film is smooth after applied. The good leveling surface should have no irregularities such as orange peel, brush marks, corrugations, and shrinkage holes. Normally, people directly observe the naked eye by comparing the sample with the standard sample to evaluate the level of coating film leveling. This method varies from person to person and has strong subjectivity. The wavelength scanning method used in the automotive industry to characterize the surface state of the coating film has a semi-quantitative effect. Long-wave (10-0.6 mm) and short-wave (0.6-0.1 mm) scans are used, and the measured value is between 0 and 100. The lower the value, the smoother the coating surface and the better the leveling.
The factors affecting the leveling property of powder coatings mainly include five aspects:
First, the melt viscosity of powder coatings
For thermosetting powder coatings, in the melt flow process, with the cross-link curing reaction, the higher the temperature, the faster the curing reaction, the faster the viscosity of the system rises, the shorter the flow time, and the less leveling. Therefore, when selecting a resin, we choose a resin with a lower viscosity, which reflects the slower activity, so that the coating can have sufficient time to level off.
Second, leveling additives
Appropriate leveling aids are added to the powder coating formulation. When the powder coating is melted, these additives can rapidly reduce the surface tension of the coating, promote rapid flow of the coating before curing and eliminate or reduce orange peel, brush marks, and ripples. , Shrinkage and other surface defects.
Third, the choice of pigment
Before matching colors, we must not only match the hue of various colors, but also consider the oil absorption and the amount of each pigment. The oil absorption of inorganic pigments is much smaller than that of organic pigments, so we can try to avoid the use of organic pigments. The total proportion of various pigments should be adjusted according to the customers’ requirements for covering. Even if the pigment with low oil absorption, excessive would cause the leveling to deteriorate.
Fourth, the choice of filler
It is well-known that fillers in powder coatings not only reduce costs but also improve the properties of powder coatings, especially wear resistance. However, improper filler will give the powder a fatal blow. In general, the oil absorption of barium sulfate is smaller than that of calcium carbonate, kaolin, mica powder, quartz powder, silicon powder, etc. The finer the diameter and the higher the gloss, the finer the particle size of other fillers, the greater the oil absorption and the poorer the leveling.
Fifth, the curing process
There is a temperature-rise process when the powder coating is baked. The speed of the heating rate has a very important influence on the leveling of the coating.
In short, considering the overall formula structure, we must first select the low-viscosity, slow-responsive resin as the main base material, adding a sufficient amount of leveling agent, and use pigments and filer (barium sulfate) with low oil absorption. In addition, the process parameters are adjusted appropriately in the process of extrusion and milling to achieve a more appearance property.
Comments are Closed