Mastering Powder Coating Particle Size Distribution: Key Metrics and Optimization Strategies
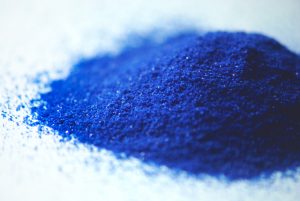
In the realm of modern industrial coating, powder coatings are steadily becoming the preferred choice due to their eco-friendly, solvent-free characteristics. The particle size distribution of powder coatings is a core technical indicator that directly affects the appearance, performance, and application results of the coating. This article delves into the importance of particle size distribution in powder coatings, measurement methods, and how to enhance their performance through optimization strategies.
Introduction
The particle size distribution of powder coatings is a critical factor influencing their coating performance, storage stability, and the quality of the final coating layer. Both overly broad and overly narrow particle size distributions can adversely affect the final coating effect. Therefore, precise control of the particle size distribution in powder coatings is essential for ensuring coating quality.
Impact of Particle Size Distribution
The uniformity of particle size distribution directly affects the leveling properties of the coating, the uniformity of the film, and the physical properties of the coating. An overly broad particle size distribution may lead to defects such as orange peel and pinholes in the film, affecting the aesthetics and durability of the coating. Conversely, an overly narrow distribution may result in poor powder flow during the coating process, impacting coating efficiency and the uniformity of the coating thickness.
Measurement and Analysis
The measurement of particle size distribution in powder coatings typically involves laser diffraction, sieving, and microscopy methods. Laser diffraction measures the scattering angle of particles by laser to calculate particle size, offering rapid and accurate results, making it the most commonly used method for particle size distribution measurement. Sieving uses sieves with different mesh sizes to separate particles of varying sizes, suitable for larger particles. Microscopy directly observes particle size and shape, ideal for scenarios requiring specific particle size distribution criteria.
Optimization Strategies
To optimize the particle size distribution of powder coatings, consider the following approaches:
Case Study
Showcase the effectiveness of optimizing particle size distribution through real-world examples. For instance, during the coating process of certain automotive components, by adjusting the grinding process and classification treatment, the particle size distribution was successfully controlled within an ideal range, significantly enhancing the leveling properties and durability of the coating.
Conclusion and Outlook
In summary, precise control of the particle size distribution in powder coatings is key to improving coating quality. The measurement methods and optimization strategies provided in this article aim to assist manufacturers and coating engineers in achieving more efficient production processes and higher-quality coating results. With continuous technological advancements, we anticipate that powder coating particle size distribution control technology will reach new heights, meeting the growing demands of industrial coating applications.