Procedure of Measurement of coating thickness- ISO 2360
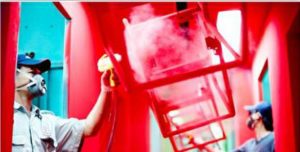
6 Procedure of Measurement of coating thickness
6.1 Calibration of instruments
6.1.1 General
Before use, each instrument shall be calibrated in accordance with the manufacturer’s instructions, using suitable calibration standards. Particular attention shall be paid to the description given in Clause 3 and to the factors described in Clause 5. In order to minimize conductivity changes due to temperature variations, at the time of calibration the instrument and the calibration standards shall be at a temperature close to the temperature of the items to be measured.
NOTE Calibration checks should also be carried out as necessary during the determinations to avoid instrument drift.
6.1.2 Calibration standards
Instrument calibration shall be made using at least two standards of different and known thicknesses. One of these standards may be of the uncoated basis material.
NOTE 1 Such standards should have their thicknesses traceable to a certifiable source.
The electrical conductivity and magnetic permeability of both coating and basis materials shall be identical to those properties of the parts to be measured.
NOTE 2 As calibration standards are subject to wear and deterioration with time and use, they should be recalibrated and/or replaced periodically at time intervals established locally or after consultation with the manufacturer.
6.1.3 Verification
The electrical properties of the basis material of the calibration standards shall be similar to those of the basis material of the test specimen.
NOTE To confirm their suitability, the readings obtained with the basis material of the uncoated calibration standard and with that of the test specimen should be compared.
If the basis material thickness exceeds the critical thickness, as defined in 5.3, the thickness measurement is not affected by the thickness of the basis material.
If the critical thickness is not exceeded, the thickness of the basis material for the test and for the calibration shall be the same. If, under practical conditions, this is not possible then it may be possible to back either the standard or the test specimen with a sufficient thickness of a material having similar electrical properties to make the readings independent of the basis material thickness. If this method is used, tests shall be undertaken to confirm that it is acceptable and to establish the presence of any additional errors.If the curvature of the coated surface to be measured is such as to preclude calibration on a flat surface, the standards used for calibration shall have the same radii of curvature as the specimen to be measured, unless a special probe that compensates for the curvature influence is used.
6.2 Determination
6.2.1 General
Operate each instrument in accordance with the manufacturer’s instructions, giving appropriate attention to the factors given in Clause 5.
Check the calibration of the instrument, using valid calibration standards, at the test site each time the instrument is put into service and at frequent intervals during use (at least once per hour) to ensure proper performance (see 6.1).
The precautions listed in 6.2.2 to 6.2.6 shall be observed.
6.2.2 Surface cleanliness
Before making measurements, remove any foreign matter such as dirt, oil, grease and corrosion products from the surface of standards and test specimen, without removing any coating material.
6.2.3 Basis metal thickness
Check that the basis material exceeds the critical thickness (see 5.3). If it does not, either use the back-up method described in 6.1.3 or ensure that the calibration was carried out on a calibration standard having the same thickness and electrical properties as the test specimen.
6.2.4 Edge effects
Do not make measurements close to an edge, hole, inside corner, etc., of a test specimen unless the validity of the calibration for such measurements has been demonstrated (see Annex B).
6.2.5 Curvature
Do not make measurements on a curved surface of a test specimen, unless the validity of the calibration for such measurements has been demonstrated.
6.2.6 Number of readings
A number of measurements made on the same spot, if necessary using a probe jig, will provide information on the repeatability (standard deviation) of the instrument and its probe at that time and at the thickness being measured.
NOTE A coefficient of variation, V, can be calculated from this standard deviation. V can be applied to a range of thicknesses.
A number of measurements made by moving the probe between each measurement, and within a specified area on the coated surface, will provide information on the repeatability of the instrument and coating within that specified area.
If a coating surface is rough or the test specimens are known to have large thickness gradients across their surfaces (e.g. because of size and/or shape) the origins of measurement variations should be established by multiple measurements.
Comments are Closed