Powder Coating Manufacturing
now browsing by tag
Applications and Future Trends of High-Quality Powder Coatings
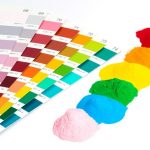
With the increasing global environmental awareness, powder coating has become the preferred material for many manufacturing industries, used in various fields such as automotive, construction, furniture, appliances, and more. In the past few decades, this industry has undergone tremendous changes and technological advances. This article will delve deep into the applications and future trends of high-quality powder coatings. Applications of Powder Coatings The application of powder coatings is very diverse, and below are some of the main areas. Automotive: PowderRead More …
Jinhu Color Powder Coating will attend the 133rd Canton Fair
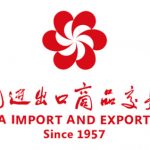
The Canton Fair is the pinnacle of international trade events, boasting an impressive history and staggering scale. Exhibiting a vast array of products, it attracts buyers from all over the world and has generated immense business dealings in China. The enormous size and scope of the Canton Fair is a biannual event for almost everything import and export with China. More than 25000 exhibitors come from all over the world to attend this twice-yearly market in Guangzhou that hasRead More …
Powder coating manufacturers prospect to the growth of powder coating demand
According to analysis by market research firm Frost & Sullivan,rapid growth of key application segments in the Asia-Pacific(APAC)and Rest of the World markets is accelerating demand for high-performance and sustainable powder coatings. With economic contraction and saturation in European and North American markets, demand is shifting to APAC. Powder coating manufacturers will be wise to target this region, as it is the strongest regional market in the construction industry, accounting for approximately 40% of global construction spending. APAC is expectedRead More …
Relating Extender Size to Gloss
As discussed, the particle size of the extender is important in controlling both gloss and gloss retention during drying of the coating film. This is illustrated , where the 20° gloss measured for a decorative alkyd gloss paint is shown as a function of drying time for different barium sulphate grades. The total PVC for this paint system was 21.5% (including the extender), with a primary pigment volume concentration of 2.5%. The gloss value increases significantly as the extender Dv97Read More …
Powder coatings manufacturing process
Powder coatings manufacturing process The process of powder coatings production includes the following steps: Distribution of raw material Pre-mixing of raw material Extrusion (mixing of melted raw materials) Cooling and crushing the extruder’s output Grinding , classifying, and controlling of the particles Packaging Pre-mixing of raw materials In this step, the distributed raw materials of each production unit will be mixed based on the guidelines and formulization of research and development unit in order to have a homogeneous mixture under specific time conditions. Extrusion The homogeneous mixture of raw materials will be melted and mixed in the extruder machine under the pressure of spiral driver and temperature of electric bars. Then , the homogeneous melted mixture will come out of the extruder while controlling the temperature of different parts of the extruder . The cooling belt The melted mixture will be poured on the cooling rollers at the temperatures between 7 C and 10 C ,formed as sheets ,carried toward the crusher through the cooling belt, and finally ,changed into chips and prepared for grinding . Grinding and sifting The produced chips at the end of cooling belt will be transferred into a mill with a pin disk. The controlling and size measuring of the ground particles will be conducted by a classifier ; the size of output particles of the mill will be measured through checking the speed of the classifier ,the speed of mill’s router and remaining of the chips inside the mill, and controlling the air volume and the temperature of the conveyer of ground powders. Based on their sizer, the output powders of the classifier and the mill will be categorized into three parts: The part of very small particles ,smaller than 10 micron , will be separated in the silicone and transferred into a container of small particles and dusts ; the remaining particles will be transferred into a sieve located at the bottom of the silicone. The ultimate product will be packaged based on the size of the net ; the net separates the inadequate and big particles. Finally , those big particles will be sent back into the mill once again through a channel devised near the sieve . In the process of coatings circulation , an additive will be added to the coating during its grinding in the mill . Quality control unit The quality control unit, founded to control the quality of products , takes out soome samples during various stages of production , such as coating chips, coatings,and coating powders , and runs various experiments using modern laboratory equipments to control the expected technical features and ensure the quality of output products.
Comparison of Cyclone recycling and Filter recycling in powder coating manufacturing
Cyclone recycling Simple construction. Simple cleaning. Effectiveness of separation depends to a large extent on operating conditions. Can produce considerable waste. Filter recycling All powder is recycled. Accumulation of fine-grained particles. May produce problems with spraying process, particularly with friction charging. Extensive cleaning: filter change requirement between colors.
Micro-particles of powder coatings to optimize the coating process
Japanese paint company developed an average particle size range between 20 ~ 40μm particles of powder coatings has been patented, ready to officially expand its market. The powder coating is the durability of good varieties, and the appearance of the coating is less than the solvent-based paint. In general, the smaller the powder particle size, and its aesthetic appearance of the coating, the better, but more than one of content than the average particle size of micro-powder coating application efficiency willRead More …
Production process of powder coatings
Premix The different dry raw materials (resin, hardener, pigment, additive, filler) are weighed in exact quantity and put in a container. This container will be tumbled or mixed during a determined time so that the raw materials are well mixed. A rather homogeneous distribution is obtained. The container is brought to the extruder, after control on homogeneity. Extrusion In the extruder, ingredients are warmed up to a sort of paste, mixed and kneaded. On molecular scale resin and hardener willRead More …
Five categories of additives in the compostion of powder coatings
This collective name for a big group of additives, to realise determined properties of the coating.5 categories exist : Accelerators (to accelerate the reaction of the curing system) Degassing additives (to let escape enclosed gases through the pores of the coating by opening them longer) Thixotropic additives (to resist sagging outs = viscosity regulator) Flow-control agent (to improve the flow on the surface) Matting agent (to reduce the gloss of powder coatings)