powder coating pretreatment
now browsing by tag
Powder Coating Surface preparation – CLEANING ALUMINUM
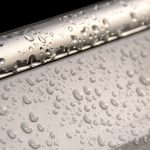
Alkaline Cleaners Alkaline cleaners for aluminum differ from those used for steel; they usually have a blend of mild alkaline salts to avoid attacking the aluminum surface. In some cases, a small to moderate amount of free caustic soda may be present in the cleaner to remove difficult soils, or to provide a desired etch. In the power spray method of application, the parts to be cleaned are suspended in a tunnel while the cleaning solution is pumped from aRead More …
Conversion Coating of Galvanized Steel
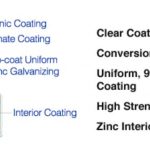
Iron phosphates or cleaner-coater products produce little or non-detectable conversion coatings on zinc surfaces. Many multimetal finishing lines use modified iron phosphates which offer cleaning, and leave micro-chemical etch on zinc substrates to provide adhesion properties. Many municipalities and states now have limits on zinc PPMs, forcing metal finishers to provide treatment of any solutions in which zinc substrates are processed. The zinc phosphate conversion coating is, perhaps, the highest quality coating that can be produced on a galvanized surface. ToRead More …
Chemical surface preparation before powder coating
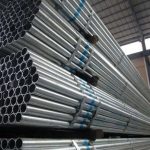
Particular application is closely related to the nature of the surface being cleaned and the nature of the contamination. Most surfaces powder coated after cleaning are either galvanized steel, steel, or aluminum. Since not all chemical-type preparations are applicable to all these materials, the preparation process selected depends on the substrate material. For each material, the type of cleaning will be discussed and its unique features for that substrate will be explained. Specific application processes are quite similar for eachRead More …
Cleaning functions most importantly in maximizing powder coating results

The highest quality powder coating will provide excellent results only if the pretreatment (cleaning, phosphatizing, conversion coating) is done correctly and the overall pretreatment system is maintained up to its potential. Powder coating brings pretreatment back to the basics of cleaning, rinsing, phosphatizing,and seal rinsing. To maximize the benefit derived from powder, the pretreatment system must provide a clean conversion coated product in a dry state to the powder booth. Surface preparation encompasses more than conditioning or improving a substrateRead More …
Phosphate coatings-the recognised pre-treatment for steel substrates
The recognised pre-treatment for steel substrates just prior to application of powder is phosphating which can vary in coating weight. The greater the conversion coating weight the greater the degree of corrosion resistance achieved; the lower the coating weight the better the mechanical properties. It is therefore necessary to select a compromise between mechanical properties and corrosion resistance. High phosphate coating weights can give trouble with powder coatings in that crystal fracture can occur when the coating is subjected toRead More …
Considerations for Choosing a Coolant for metal working process
Different metal working processes have varying cooling and lubrication needs. Coolants have many properties that increase their efficiency, extend their life, and minimize the potential to damage tools and products. Therefore, when choosing a coolant, many factors need to be considered. These considerations include: Tramp oil rejection Ability to settle out solids Bacterial resistance Corrosion and rust resistance Emulsification capability Foaming nature and resistance Optimal coolant life Longevity of coolant as measured against current industrial standards Cost of coolant ChemicalRead More …
Paint Removal
When repainting a part,prior to application of the new paint coat the old,paint often must be removed. The waste reduction assessment should start by examining what causes the need for repainting: inadequate initial part preparation; defects in coating application; equipment problems; or coating damage due to improper handling. While no process is perfect, reducing the need for repainting has a direct effect on the volume of waste generated from paint removal. Once the need for paint stripping has been reducedRead More …
Definitions for corrosion classification
As an aid in finding what requirements should be made for pre-treatment, we can define different corrosion classification: Corrosion Class 0 Indoors with relative humidity over 60% Very little corrosion risk (aggressivity) CORROSION CLASS 1 Indoors in non-heated, well ventilated room Little corrosion risk (aggressivity) Corrosion Class 2 Indoors with fluctuating temperature and humidity. Outdoors in inland climates, far from sea and industry. Medium corrosion risk (aggressivity) CORROSION CLASS 3 In densely populated areas or near industrial areas. Above open waterRead More …
Filiform corrosion is special kind of corrosion appearing mostly on aluminum
Filiform corrosion is special kind of corrosion appearing mostly on aluminum. The phenomenon resembles a worm creeping under the coating, always starting from a cut edge or a damage in the layer. Filiform corrosion develops easily when the coated object is exposed to salt in combination with temperatures 30/40°C and relative humidity 60-90%. This problem is therefore limited to coastal areas and linked with unfortunate combination of aluminum alloys and pre-treatment. To minimize filiform corrosion it is advised to ensure aRead More …
Phosphate treatment for powder coating
Iron phosphate Treatment with iron phosphate (often called thin layer phosphating) provides very good adhesion properties and has no adverse effects in the mechanical properties of the powder coating. Iron phosphate provides good corrosion protection for exposure in the low and middle corrosion classes, though it cannot compete with zinc phosphate in this respect. Iron phosphate can be used in either spray or dip facilities. The number of steps in the process may vary from 2-7, depending on the basemetalRead More …