Powder Coating News
now browsing by category
Hot news ,developing ,technology of powder coating industry .
Global Coil Coatings Market Expected to Surpass 6% CAGR during 2016-2020
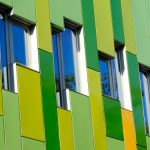
According to a new market research report released by Technavio, a research institute, the global compound coating growth rate for the global coil coating market is expected to exceed 6% during 2016-2020, which is a significant increase. The study pointed out that the construction industry is the largest application area for coil coatings (accounting for approximately 76.4%), and it is also the most important factor to stimulate the development of the global coil coating market. In addition, users in theRead More …
Welcome to Coatings Expo Vietnam 13-15/6/2018
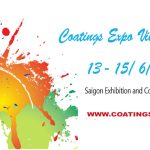
“FEIHONG Powder” hereby sincerely invite you or your company representative to visit our booth in COATINGS EXPO VIETNAM 13-15/6/2018 . Exhibition Addreee: Saigon Exhibition and Convention Center (SECC) 799 Nguyen Van Linh, Tan Phu Ward, Dist 7. Ho Chi Minh City Booth Number: R19 Date: June 13-15, 2018 Coatings Vietnam Expo 2018 is one of the most attractive annual international events in Viet Nam. This will be a chance to all the coating enterprises for not only meeting and exchangeRead More …
CSA Z245.20-02 External Fusion Bond Epoxy Coating for Steel Pipe
Related Product for Sale: FBE Powder Coating Related Articles: FBE Powder Coating
Factors affecting the leveling property of powder coatings
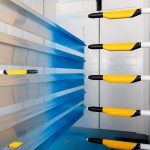
Powder coating is a new type of solvent-free 100% solid powder coating. It has two main categories: thermoplastic powder coatings and thermosetting powder coatings. The paint is made of resin, pigment, filler, curing agent and other auxiliaries, mixed in a certain proportion, and then prepared by hot extrusion and sifting and sieving. They are stored at room temperature, stable, electrostatic spraying or fluidized bed dip coating, reheating and baking melt solidification, so that the formation of a smooth and long-lastingRead More …
Application of Self-Healing Coating Technology in Powder Coatings
Since 2017, many new chemical suppliers entering the powder coating industry provided new assistance for the advancement of powder coating technology. The coating self-healing technology from Autonomic Materials Inc. (AMI) provides a solution to the increased corrosion resistance of epoxy powder coatings. The coating self-healing technology is based on a microcapsule with a core-shell structure developed by AMI and can be repaired when the coating is damaged. This microcapsule is post-mixed In the preparation of powder coating process . OnceRead More …
The relocation of the company sales office
Dear FRIENDS,PARTNERS, After years of steady development of the company, especially the company’s scale continues to grow and develop, the original sales office location can no longer meet the company’s development needs. After the concerted efforts of all the company’s colleagues, Jinhu Color Powder Coating Co.Ltd successfully completed the relocation of the new site of sales office and resumed normal work on March 30, 2018. The new site of the office is:RM1004, No.1 Yu Hu Guo Ji,No.153 Long Pan Road,Read More …
Attend 123th Import and Export Fair (Canton Fair) in April 15-20,2018
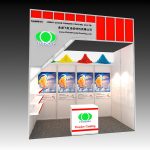
Dear Sir/Madam, Will you take part in the 123th China Import and Export Fair (Canton Fair) in Guangzhou city,China ? “FEIHONG” hereby sincerely invite you or your company representative to visit our booth from April 15-20 . “FEIHONG” is one of the leading manufacturers of powder coating in China,it would be a great pleasure to meet you at the exhibtion. Exhibition Hall: C Booth Number: 14.4I40-41 Date: April 15-20 Regards! Internation Trade Dept. Invitation Application
Coating Shows 2018 Worldwide
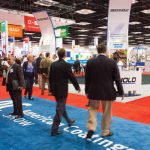
Pakistan Coating Show 18-20 Jan 2018 Lahore International Expo Centre, Lahore, Pakistan The largest congress in this field in Pakistan Interlakokraska Moscow 27 Feb-02 Mar 2018 Expocentre, Moscow, Russia TURKCOAT & PaintIstanbul 2018 22-24 Mar 2018 Istanbul Fuar Merkezi, Hall 9-10-11-FOYER COATING KOREA 2018 International Coating, Adhesive and Film Fair 2018 2018.3.28(Wed) ~ 3.30(Fri) (3days) Songdo Convensia,Incheon, Korea American Coatings SHOW April 10-12, 2018 INDIANA Convention Center,100 S. Capitol Ave.Indianapolis,IN 46225
Visit us in CHINACOAT 2017 ( NOV15-17 )
We invite you to visit us in CHINACOAT 2017, this exhibition is scheduled to be held Nov 15-17, Shanghai, China. Hall No.: E2 Zone No.: 3 Booth No.: E2.H45 Attached please see the Floor Plan for Powder Coating Zone CHINACOAT has been organized since 1996 and now alternates its venue city annually between Guangzhou and Shanghai, P. R. China. It is the world’s Coatings show and a key event for industry players from all around the world. In 2017, CHINACOATRead More …